その他のトラブル
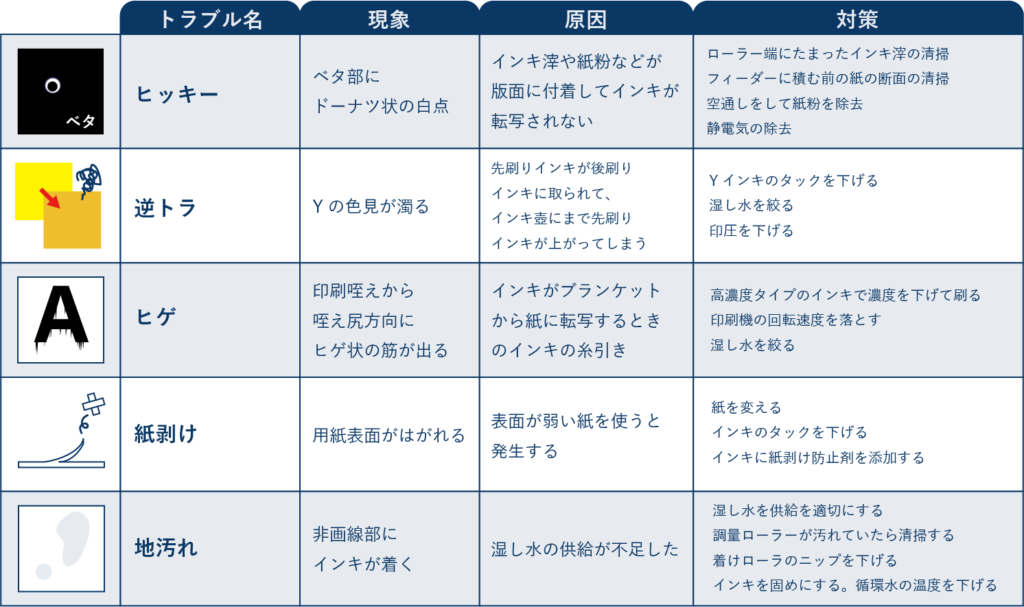
印刷トラブルは複合的な原因で起こる。
インキは版面から紙に転写して機械の外に出ていく。紙に転写される以外に機械の外に出ていくことはない。
従って、絵柄が極端に少ない場合、インカーから出ていくインキ量は非常に少なく、インキキーで制御しても版面に供給されるインキ量は過剰になりやすい。
すると、古いインキが版面やインキ着けローラーに残り続け、湿し水と接する時間が長くなって、乳化が進行し過乳化がおこる。インキの着きが悪くなるのでインキキーを開けると、更にインキ過剰となって悪循環となる。こういうケースになるとインキを総とっかえするしかなくなる。
絵柄が少ないのはデータの段階でわかるので、一回り大きな紙を準備して、ステベタをつける。ステベタで過剰なインキを機械の外に出してやり、常に新鮮なインキを供給すればよい。
紙を大きくするとコストが上がるが、印刷不良で追加印刷や再印刷をすることを考えれば、紙代をけちるより経済的である。
版面上ではインキと湿し水が混在するため、水棒にもインキが入ってくる。特にインキを多く使っている部分から調量ローラーが汚れてくる。調量ローラーが汚れてくると、湿し水が上がらなくなるので、水目盛を上げる。すると今度は適正だった部分に湿し水が上がりすぎ、その部分は過乳化状態に陥る。
この悪循環をさせないためにも、調量ローラーはコマメに清掃する必要がある。また、湿し水の供給が少なすぎると非画線部にもインキが着き始め、刷本全体が汚れる地汚れが起きる。
このようなことが片面カラーだと4胴で起き、両面カラーだと8胴で起こるので、オペレーターは常に刷本や機械状態を見ながら、適正な状態を保つ努力がいる。それなのに、フィーダーストップが頻出するとフィーダーにばかり注意がいって、それ以外の確認がおろそかになり、印刷トラブルを起こしやすい。
印刷機械の自動化省力化は進み、かなりの部分、機械任せでもできるようにはなったが、紙とインキと湿し水を使っていることには変わりない。
また、インキキーコントロールが自動になってもインキキーのゼロセットができていないと、折角のデータが使えない。インカーのローラーが汚れ、ローラー端にインキ滓がたまると、インキ滓が着けローラーから版面に移動し、上記のヒッキーを起こす。
ニップ幅や胴仕立が適切でないと、インキと湿し水のバランスが崩れていく。日頃のメンテナンスや清掃が非常に重要である。